Bioprocess Optimization
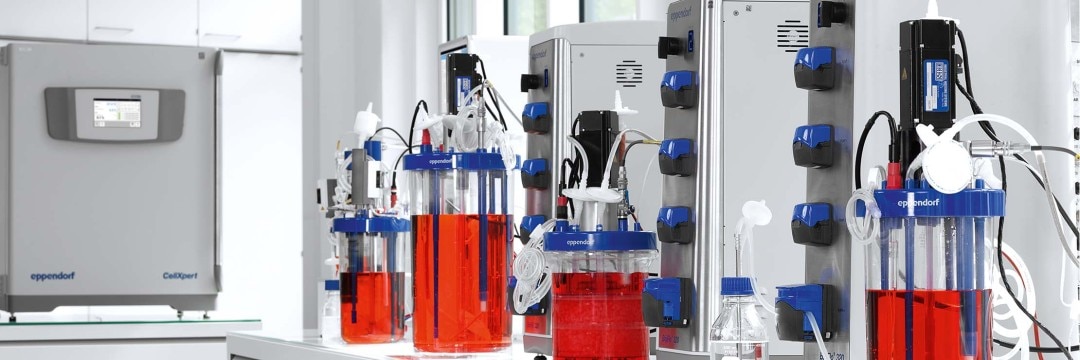
Improve reproducibility
Improve yield
Reducing batch variability and improving yield
显示更少
How can bioprocess reproducibility be improved?
显示更少
Fine control of process conditions
Fine-tuning the control of your bioprocess is critical to ensure quality, yield, and batch consistency of the product produced. You can automatically gain information about your process by implementing Process Analytical Technology (PAT). PAT can provide real-time monitoring of critical process parameters (CPPs), such as pH, DO, temperature, cell density, cell viability, nutrient concentrations, by-product concentrations, and help to keep these within a defined range. When incorporated into bioreactor control systems, PAT can be used to acquire data in real-time and use it to leverage feedback loops, for automated, in-process parameter control. For example, it is possible to automate culture feeding based upon the glucose concentration in the medium. By automating bioprocess control, stress on the cells can be reduced significantly, and form a sound foundation for optimal performance.
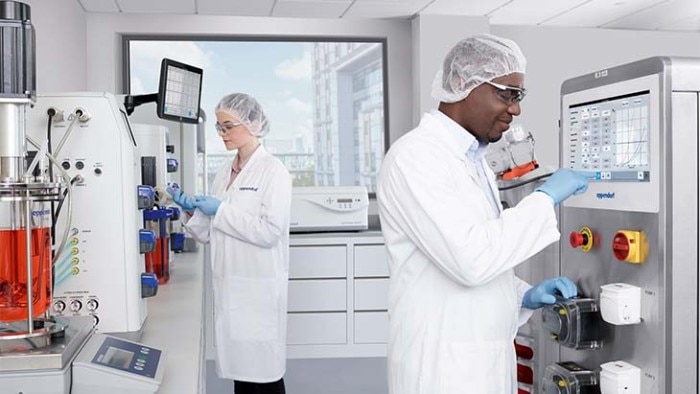
Robust calibration of sensors
显示更少
Interested in how to increase the reproducibility of cell culture bioprocesses? Check out our e-book .
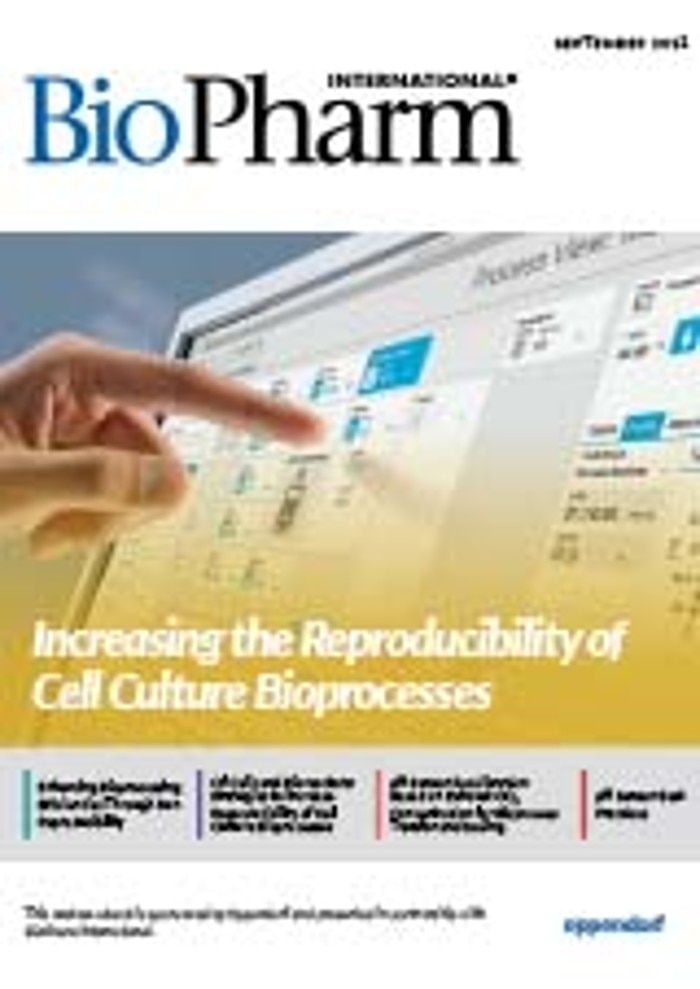
Ensuring consistent cell quality in bioreactor culture
- Monitor cell growth in your shake flask culture – Take note of your flask culture data, including cell density and metabolites. Creating a growth curve can be an effective way to see if your culture is on track.
- Optimize your passage schedule – Ensure that you split your cells at the optimal time point in their growth phase. Too frequent passaging can hinder cell density, while too infrequent will cause metabolite build up and affect viability.
- Keep your flask in optimum conditions – Ensure that flasks are kept in an incubator with optimized temperature, plus CO2, oxygen, and moisture levels. Make sure that flasks spend minimal time outside the incubator for monitoring/passage.
- Keep track of pH levels – Try and keep the pH level in the flask and in the bioreactor medium at a standard level to avoid pH shock. In-flask pH monitoring systems is useful for this.
显示更少
Want to learn more about inoculum optimization in a cell culture scale-up workflow? Check out our application note.
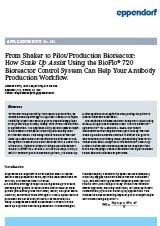
How can bioprocess yield and productivity be improved?
显示更少
Choose the best process mode for you
显示更少
Solutions for bioprocess optimization
显示更少
Eppendorf has a range of bioprocess control solutions to help you with optimizing your process, including but not limited to:
- DASbox® Mini Bioreactor System : Designed for small working volumes and parallel experimentation, it can boost your bioprocessing research and early process development.
- DASware® control bioprocess control software : Enables bioprocess monitoring and control and the integration of analytical devices to your bioreactor system. Along with the DASware® software suite, this is a valuable tool for experimental design.
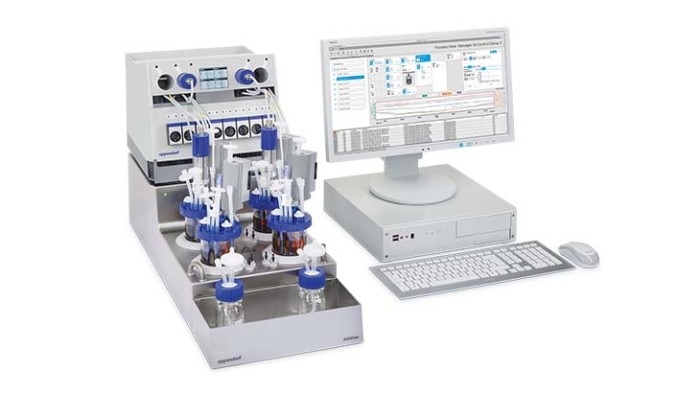